2000~2006年
第10章 苦闘を糧に、将来に向けた事業基盤の再構築
第2節 大火災の発生とリスク・コンプライアンス体制の整備
第1話 栃木工場、甘木工場の火災
栃木工場の火災の経緯
2003年9月8日午前11時40分~45分頃、栃木工場の精練工程のバンバリー3号機の発泡剤計量ライン近傍から火の手が上がりました。出火と同時に自衛消防隊が初期消火にあたりましたが、火勢が強まったことから自力消火を断念。黒磯那須消防組合や、消防庁緊急援助隊の消火活動により、3階建ての精練棟と、屋外に保管していた約16万本のタイヤを消失した後、10日の10時30分になってようやく鎮火しました。 渡邉社長は、避難した住民、近隣住民の健康不安に対する対応をしっかりすることと、農作物や水質に対する対応を、第三者も入れてしっかり行うよう指示しました。 現地では火災事故後の翌朝には苦情窓口を設けたほか、地域住民の方々の健康に対する問い合わせ等を受ける健康相談窓口を設け、産業医、看護師、保健師らが24時間体制で対応にあたりました。また、大気汚染、土壌への影響、地下水汚染などについて調査を行いましたが、いずれも大きな問題は発生しませんでした。近隣への対策は火災後も続き、きめ細かな対応を行いました。
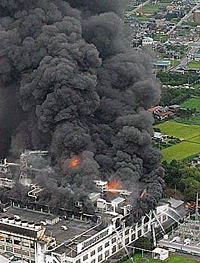
出火原因の調査
出火原因を特定するため、直ちに対策本部を設置し、火災現場調査、栃木工場の防火管理体制の確認、関係従業員からの聞き取り調査等の原因調査、各種薬品類の燃焼実験、及び再発防止策の検討を行いました。
直接の原因は、精練棟に設置されていた機器脚部の床の穴を、従業員が金属板でふさごうとして溶接作業を行ったことにありました。また、工場の防火・防災管理要領に反し、防炎シート等による防炎措置をしないまま火気を使用したことや、周辺に発泡剤が飛散していたことも、火災の原因であったことがわかりました。
防災対策の充実
当社は、再発防止のため、全社の防災統括機能として防災管理室を設置し、防災対策を充実させ、火気や危険物の管理体制を強化するなど、体制を整備しました。
一方で再発防止と従業員の防災に対する意識の向上を図るため、栃木工場内に防災センターを設けるなどして、さまざまな防災教育・訓練を実施しました。そして9月8日を「全社防災の日」と定め、毎年、全事業所で防災訓練を行い、社員の防災意識の一層の向上に努めています。
復旧への道のり
鎮火後、消防当局から報道機関に対して「安全宣言」が出され、9月20日の午後から一部生産を再開しました。
火災による損害額は、総額400億円に及びました。全社の支援により、火災による生産への影響は最小限に食い止めたものの、自動車メーカーへのタイヤ納入では、同業他社からの支援を一部仰ぐこととなりました。
渡邉社長は、栃木工場の敷地内に精練棟を再建することを表明、防火対策は監督官庁による懇切な指導のもとに慎重に行い、2004年7月に操業を開始しました。
甘木工場火災
懸命に種々の防災対策に取り組んできたにもかかわらず、栃木工場の火災から1年もたたないうちに甘木工場で火災が発生しました。2004年8月20日14時22分、精練工程で火災が発生し、消防による消火活動により、16時43分に鎮火しました。この火災では、従業員13名が病院に運ばれて治療を受けるなど、人的被害も出ました。
火災の原因は、精練工程のバンバリーミキサー内で練りゴムが高温に達していたにもかかわらず、温度センサーが温度を正常に表示せず、更に練り続けたため、ゴムが加熱して発火したものであることが判明しました。
その後、被災していないバンバリーについては8月25日に操業を再開、被災したバンバリーの修復に努め、9月には操業を再開しました。この甘木工場の火災に鑑み、当社は予防管理を一層強化し、そのための体制を敷きました。
第2話 安全、環境に関する体制の整備
安全宣言の策定
2003年7月、「ブリヂストンの安全宣言」が誕生しました。この宣言は「安全はすべてに優先する」というキャッチフレーズのもと、7つの安全基本方針で構成されています。
その後、「火災や地震などへの災害防止活動」の視点も加える改定を行い、グループ各社もこの活動に参画することになりました。
環境理念の制定と環境中長期計画の策定
2002年末、「未来のすべての子供たちが『安心』して暮らしていけるために」と題した「環境理念」を制定し、次の通り宣言しました。
「ブリヂストングループ」は、社会から信頼され、自らも誇れる企業となることを目指し、持続可能な循環型社会の実現に向けて、地球環境の保全及び多様な生活者一人ひとりの安全と健康に配慮した企業活動を推進します。
そして、2003年度を「環境経営元年」として位置付け、「環境中長期計画」に則り、多彩かつ具体的な活動を推進しました。
- 1国内15工場でゼロ・エミッション達成
当社では産業廃棄物の最終処分量を発生量に対して1%未満にすることを「ゼロ・エミッション」と位置付け、1999年から取り組みに着手した結果、2004年7月に国内全15工場でゼロ・エミッションを達成しました。また、第2ステップとして、全ての産業廃棄物について、品目ごとに再資源化の委託契約の締結を完了することを定義づけた「完全ゼロ・エミッション」を、2005年6月に国内全15工場で達成しました。 - 2臭気対策
タイヤ工場の臭気低減のため、工程の改善や脱臭装置導入を行い、臭気に対する苦情の減少に努めてきました。現在は臭気の高精度分析を行い、臭気成分に対する消臭技術の研究・開発などに取り組んでいます。 - 3ISO14001統合認証取得
1997年に東京工場が、ISO14001の認証を国内タイヤメーカーとしては初めて取得しました。また、2001年末には国内の全工場がISO14001の認証を取得しました。
その後、グローバル統一環境経営システム「TEAMS(Total Environmental Advanced Management System)」の構築を進め、2005年12月、生産事業所と本社・支店、技術センターの国内23拠点を合わせたISO14001全社統合認証を取得しました。 - 4その他の環境対策
廃タイヤを道路舗装に利用する技術開発等、廃タイヤリサイクルにも取り組んできました。 また、地球温暖化防止対策の一つとして、コ・ジェネレーションシステム※の導入も進めてきました。1995年の東京工場への導入を皮切りに各工場で採用し、2005年の防府工場への導入をもって国内の全タイヤ工場での導入が完了しました。
※燃料により発電するとともに、その際に発生する排熱を冷暖房や給湯、蒸気などに有効利用する省エネルギーシステム。